Understanding 1mm 202 Core Rubber Flex Factories A Comprehensive Insight
In the realm of industrial manufacturing, 1mm 202 Core Rubber Flex factories play a pivotal role in producing high-quality flexible rubber materials that cater to a diverse range of applications. These specialized facilities are dedicated to crafting rubber compounds with a specific focus on 1mm thickness and a 202 core structure, ensuring exceptional durability, flexibility, and resilience.
The '202 core' refers to a particular type of rubber composition, often characterized by its superior strength and elasticity. It is designed to withstand extreme environmental conditions, mechanical stress, and continuous flexing without losing its inherent properties. This makes it an ideal choice for industries such as automotive, aerospace, construction, and electrical, where robust and adaptable materials are crucial.
1mm 202 Core Rubber Flex factories employ state-of-the-art technology and advanced machinery to manufacture these rubber products. The process begins with the selection of raw materials, which typically includes natural rubber, synthetic rubber, or a blend of both. These ingredients are then mixed, refined, and vulcanized to create the desired 1mm thickness and 202 core structure. Vulcanization, a heat treatment process, imparts the necessary physical properties to the rubber, making it more durable and resistant to wear and tear.
Quality control is a paramount aspect of operations in these factories. Rigorous testing is conducted at every stage of production, from the initial mixing to the final product, to ensure compliance with industry standards and customer specifications Rigorous testing is conducted at every stage of production, from the initial mixing to the final product, to ensure compliance with industry standards and customer specifications
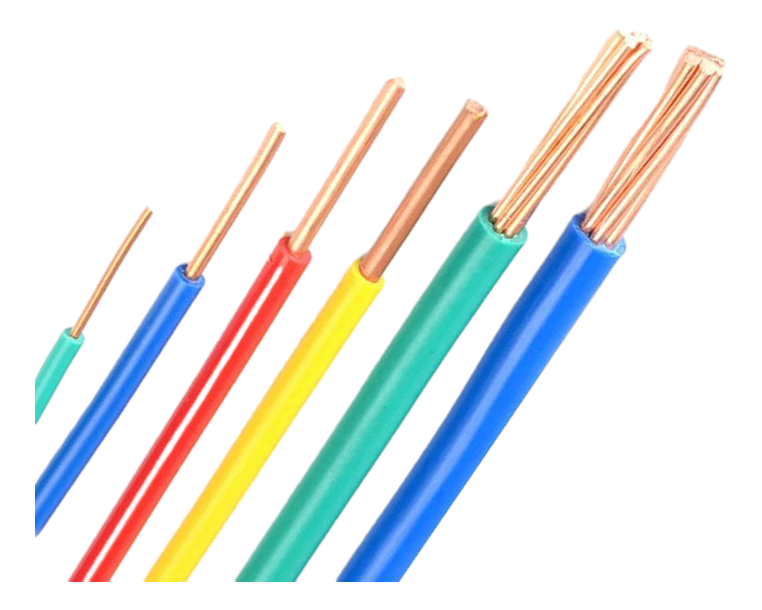
Rigorous testing is conducted at every stage of production, from the initial mixing to the final product, to ensure compliance with industry standards and customer specifications Rigorous testing is conducted at every stage of production, from the initial mixing to the final product, to ensure compliance with industry standards and customer specifications
1mm 2 core rubber flex factories. Tests include tensile strength, elongation, hardness, and temperature resistance, among others. This meticulous attention to detail guarantees the consistency and reliability of the manufactured rubber flex.
Environmental sustainability is also a growing concern in the rubber industry, and 1mm 202 Core Rubber Flex factories are increasingly adopting eco-friendly practices. This includes using recyclable materials, optimizing energy consumption, and implementing waste management strategies to minimize their carbon footprint.
Furthermore, these factories often collaborate closely with clients, providing customized solutions tailored to their unique requirements. Whether it's for seals, gaskets, hoses, or any other application requiring flexible rubber parts, these factories have the expertise and resources to deliver precision-engineered products.
In conclusion, 1mm 202 Core Rubber Flex factories represent the intersection of innovation, precision engineering, and sustainable manufacturing practices. Their commitment to producing high-performance rubber components ensures that industries across the globe can rely on these materials for their critical applications. As technology continues to evolve, these factories will undoubtedly continue to push the boundaries of rubber engineering, driving progress in various sectors.