The Evolution and Challenges of Resistant Cable Factories
In the ever-evolving landscape of industrial manufacturing, resistant cable factories have played a pivotal role in shaping the backbone of modern infrastructure. These specialized facilities produce cables designed to withstand harsh environmental conditions, providing critical links for everything from telecommunications to power transmission. As technology advances and demands increase, these factories face unique challenges that test their resilience and adaptability.
The history of resistant cable factories is marked by innovation and adaptation. Early cables were susceptible to damage from weather, rodents, and physical stress, leading to costly breakdowns and maintenance. In response, manufacturers developed more durable materials and construction techniques. Today's resistant cables are made with high-grade insulation, protective sheaths, and reinforced cores, ensuring they can endure extreme temperatures, moisture, and mechanical strain.
However, producing such robust cables is no small feat. Resistant cable factories must maintain rigorous quality control standards, employ skilled technicians, and invest in cutting-edge machinery. They also need to stay abreast of changing industry regulations and performance specifications. This constant pursuit of improvement requires significant financial resources and a commitment to research and development.
Environmental concerns have also come to the forefront for these factories. As the push for sustainability grows, there is increasing pressure to reduce the ecological footprint of cable production. This involves finding ways to minimize waste, using recycled materials where possible, and developing energy-efficient manufacturing processes This involves finding ways to minimize waste, using recycled materials where possible, and developing energy-efficient manufacturing processes
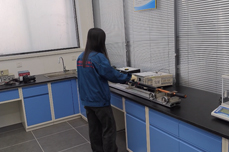
This involves finding ways to minimize waste, using recycled materials where possible, and developing energy-efficient manufacturing processes This involves finding ways to minimize waste, using recycled materials where possible, and developing energy-efficient manufacturing processes
resistant cable factories. For many factories, this transition represents a substantial operational shift that necessitates both capital investment and cultural change within the organization.
Moreover, resistant cable factories must navigate an increasingly competitive global market. As countries like China and India emerge as major producers of cables, established manufacturers face stiff price competition. To maintain market share, these factories need to balance cost-effectiveness with quality, often by adopting lean manufacturing principles and streamlining supply chains.
Despite these challenges, the future for resistant cable factories remains bright. Advancements in materials science promise even more durable and efficient cable designs. Smart factories, leveraging Internet of Things (IoT) technologies, are beginning to transform production lines, making them more flexible and responsive to customer needs. And as societies continue to electrify and digitize, the demand for reliable cable systems shows no signs of abating.
In conclusion, resistant cable factories stand at the intersection of innovation, environmental stewardship, and economic pragmatism. Their ability to evolve amidst technological advancements, regulatory mandates, and competitive forces will determine not only their own success but also their contribution to the larger infrastructure that underpins modern civilization. As long as our world relies on power and data transmission, the work of these factories will remain vital—and their resilience continually tested.