Custom Electrical Cables for Outdoor Use
In the world of electrical infrastructure, custom cables designed for outdoor use are a specialized niche that requires meticulous attention to detail and robustness. These cables are engineered to withstand the harsh conditions that outdoor environments can present, from extreme temperatures to moisture, UV radiation, and mechanical stresses. The ingenuity behind custom electrical cables for outdoor applications is not only in their ability to conduct electricity reliably but also in their adaptability to various sectors such as construction, mining, renewable energy, and telecommunications.
The core of these cables often consists of high-quality copper or aluminum, which are excellent conductors of electricity. However, what sets them apart is the protective layers they possess. The insulation surrounding the core wires is typically made from materials like cross-linked polyethylene (XLPE) or ethylene propylene rubber (EPR), known for their exceptional electrical properties and resistance to temperature fluctuations and chemicals. Furthermore, an additional layer of protection comes in the form of a waterproof sheath, usually made from polyvinyl chloride (PVC) or another synthetic material, providing a barrier against moisture ingress.
For scenarios where the cables might be exposed to physical damage, be it from wildlife interference or accidental impacts, the outer jacket is reinforced with an armor layer. This could be a wrap of steel wires or abrasion-resistant fabrics, ensuring the cable can endure external stress without compromising its integrity. Additionally, some custom cables are equipped with UV-resistant coatings to prevent degradation from prolonged sun exposure.
Customization extends beyond mere protection; it also encompasses specific performance requirements
Customization extends beyond mere protection; it also encompasses specific performance requirements
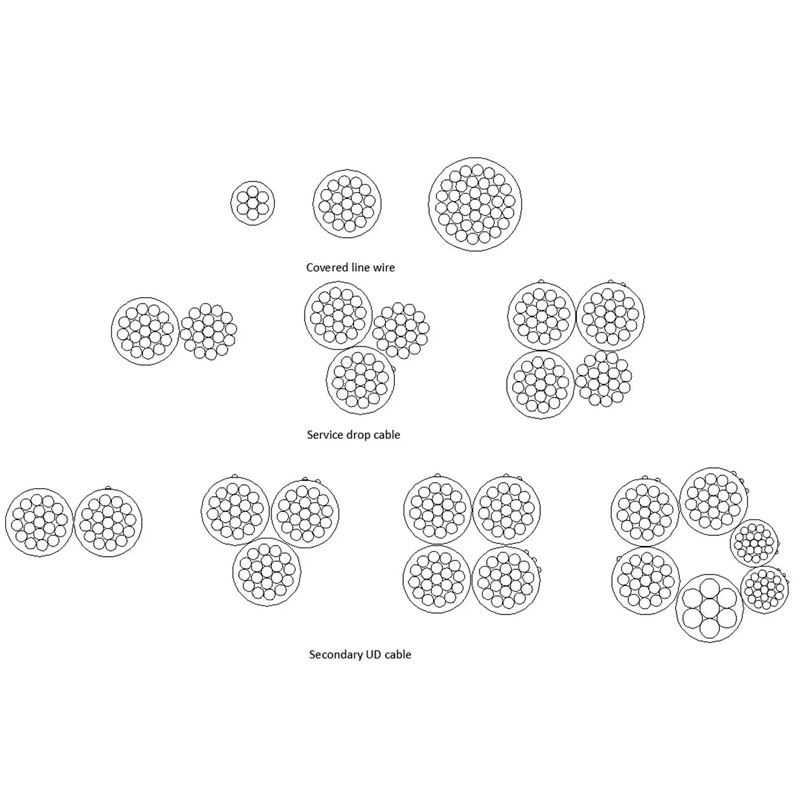
Customization extends beyond mere protection; it also encompasses specific performance requirements
Customization extends beyond mere protection; it also encompasses specific performance requirements
custom electrical cable for outdoor use. For instance, in wind farms, the cables need to be lightweight yet strong enough to withstand the dynamic forces exerted by the rotor blades. In marine applications, the cables must be resistant to saltwater corrosion and capable of flexing without breaking as waves and tides move them.
The design of connectors and terminations is equally important. They must provide a secure and watertight connection, preventing any ingress of moisture that could lead to short circuits or corrosion. Stainless steel or other corrosion-resistant materials are often used for these components, ensuring longevity in challenging outdoor conditions.
In conclusion, custom electrical cables tailored for outdoor use are a testament to human innovation in overcoming natural challenges. They embody a combination of materials science, engineering precision, and an understanding of the environment they serve. As our reliance on technology in all weathers continues to grow, so too does the necessity for these specialized cables to safely and efficiently transmit power in the great outdoors.